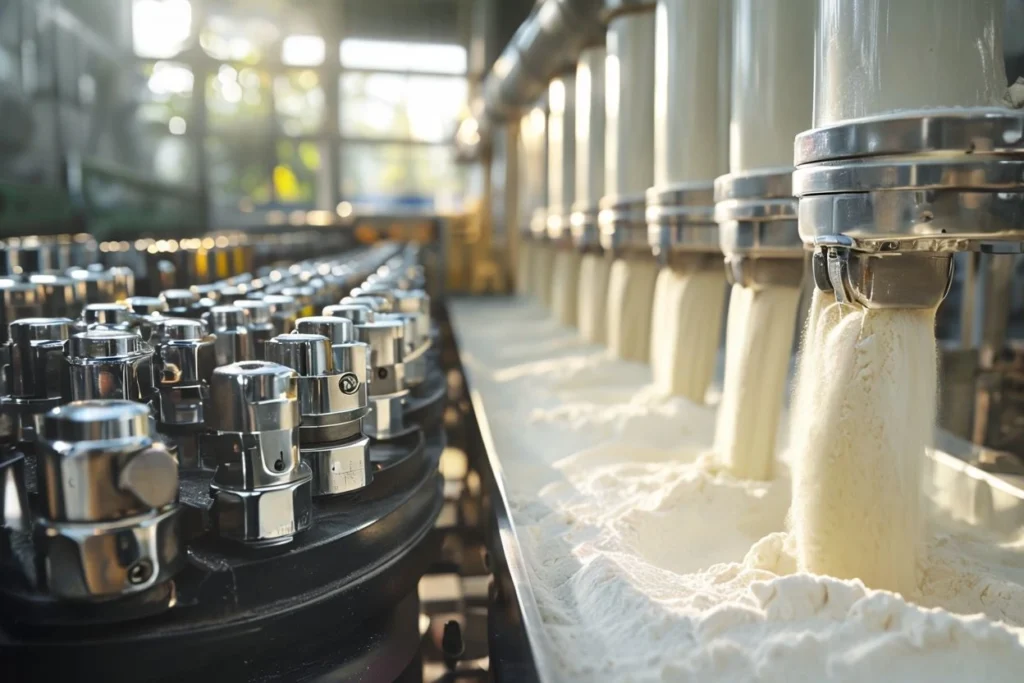
The efficiency of production processes plays a key role in optimizing production, minimizing losses, and improving productivity in both discrete and continuous processes. Understanding and properly measuring parameters such as OEE (Overall Equipment Effectiveness) enable the identification of areas requiring optimization. This article explores methods for calculating efficiency, the specifics of production processes, and the challenges associated with monitoring and improving efficiency metrics.
What are the components of efficiency in discrete and continuous production?
The OEE metric represents the overall efficiency of the equipment. It integrates three key elements that allow for assessing the actual performance of machines and production lines: availability, performance, and quality.
• Availability: Measures the time during which a machine or production line is ready for operation. Availability is calculated based on machine runtime signals, the absence of alarms, and data from operator panels. For example, if scheduled machine cleaning takes longer than planned, every additional minute reduces the availability indicator.
• Performance: Refers to the production rate in relation to the planned or technological potential of the machine. For discrete processes, it can be determined based on production cycles, while in continuous processes, the reference point is typically the optimal capacity of technological installations.
• Quality: Determines the percentage of production meeting standards. In most facilities, quality is measured post-production, for instance, based on the number of defective items compared to the total number of units produced or accepted into inventory.
The distinction between production and industrial efficiency
Notably, efficiency in production facilities can be divided into two main aspects:
1. Production efficiency: Focuses on analyzing efficiency during actual production time. This means it considers only the time when the machine is available for executing a task, and its parameters such as availability, performance, and quality are measured against the production plan. For example, if a machine signals readiness for work and production proceeds without alarms, production efficiency measures the execution of the production plan in time units.
2. Industrial efficiency: Refers to the overall analysis of the utilization of the entire machinery park, including time allocated for technological downtimes, maintenance, or preparation. For instance, in an industrial context, one analyzes how many working days in a month machines were actually used for production, regardless of the production targets set. If a plant operates for 22 days in a month, but machines were in use for only 15 days, industrial efficiency might be low, even if production efficiency during the actual operation time of the machines was high.
Efficiency in discrete processes
Discrete processes are characterized by a clear division into production units. They are often associated with the automotive industry, where individual components are assembled into larger systems. For example, the production of car engine parts involves assembling components such as pistons, crankshafts, and cylinders. Each stage is easy to monitor using production counters, and efficiency is measured in relation to the number of assembled components within a specified time frame.
Efficiency and challenges of continuous processes
Continuous processes are more complex as they involve uninterrupted material flows, such as grain milling, fluid pasteurization, or oil production. Key challenges in these processes include:
1. Lack of visible production units: Continuous processes require the use of measurement tools such as flow meters, scales, or volume counters.
2. Monitoring multi-step operations: Each stage of the process, such as mixing or pasteurization, requires a separate efficiency analysis.
3. Interdependence between stages: The flow of raw material between production stages must be smooth to avoid downtime and material losses.
Example: rapeseed oil production
In the rapeseed oil production process, the quality of the raw material is particularly important. Rapeseed entering production often contains impurities, such as stones or husks. In the initial stage, the raw material is weighed and then cleaned. The weight of the waste determines the quality of the delivered rapeseed. For example, if the supplier claims 5% waste but it actually reaches 15%, this becomes a significant issue for efficiency and production quality. Such a discrepancy necessitates renegotiating supply terms or introducing additional cleaning stages.
After the rapeseed is cleaned, the oil extraction process provides further data for efficiency analysis. The efficiency of pressing depends on the quality of the raw material and the technical parameters of the equipment. From the weight of the final oil, it is possible to determine how effectively the raw material was utilized. If the technological equipment is designed for a specific efficiency (e.g., 1 liter of oil from 5 kg of rapeseed), any deviation from these norms is carefully monitored.
Similarly, the quality of the oil can be checked at the storage stage. Comparing the weight of the final product with the initial raw material allows for calculating losses at various stages, such as cleaning, pressing, or filtration.
Efficiency in packaging processes
Packaging in continuous processes is one of the critical stages of production that requires a specific approach to monitoring efficiency. Here are the key aspects to consider:
1. Component availability: Shortages in the supply of elements such as bottles, cups, or lids directly impact the availability of the packaging line. For example, a lack of bottle caps may force the line to stop.
2. Synchronization with preceding stages: In continuous processes, it is essential to ensure the smooth flow of the product from technological stages to the packaging line. Downtime in earlier stages, such as pasteurization, can cause the packaging line to halt.
3. Quality control of packaging: Packaging quality can be measured by the number of rejected units and compliance with standards. Technical issues, such as improperly sealed bottles, can significantly reduce packaging efficiency.
Algorithms and tools supporting efficiency measurement
Modern tools such as MES (Manufacturing Execution System) and SCADA (Supervisory Control and Data Acquisition) systems allow real-time monitoring of OEE parameters. In continuous processes, algorithms based on data from flow meters and volume sensors are particularly useful. In discrete processes, production cycles and the percentage of rejected products are analyzed.
Efficiency in discrete and continuous production – examples of measurement
1. Discrete production: In the production of automotive components, such as pistons or cylinders, efficiency can be measured based on the number of assembled elements within a specific time frame, compared to the production plan.
2. Continuous production: In rapeseed oil production, each stage, from cleaning the seeds to oil extraction, is analyzed separately. By examining the flows of raw materials and the final product, actual efficiency and the quality of the extracted oil can be calculated.
Measuring the efficiency of industrial processes requires tailoring methods to the specific characteristics of discrete and continuous processes. OEE is an effective tool for identifying underutilized areas. In continuous processes, it is particularly important to monitor multi-stage material flows, while in discrete processes, precise performance calculations based on production cycles are key.
The distinction between production efficiency and industrial efficiency enables a more accurate analysis of operations and strategic planning. To effectively monitor efficiency, investing in advanced systems and utilizing appropriate reports that provide business-critical data is crucial. Implementing the right tools and strategies in this area should be the first step in digital transformation.
Contact us
Do you want to move your production plant to level 4.0? Are you interested in modern solutions for industry in the field of automation and digitisation? Be sure to let us know!